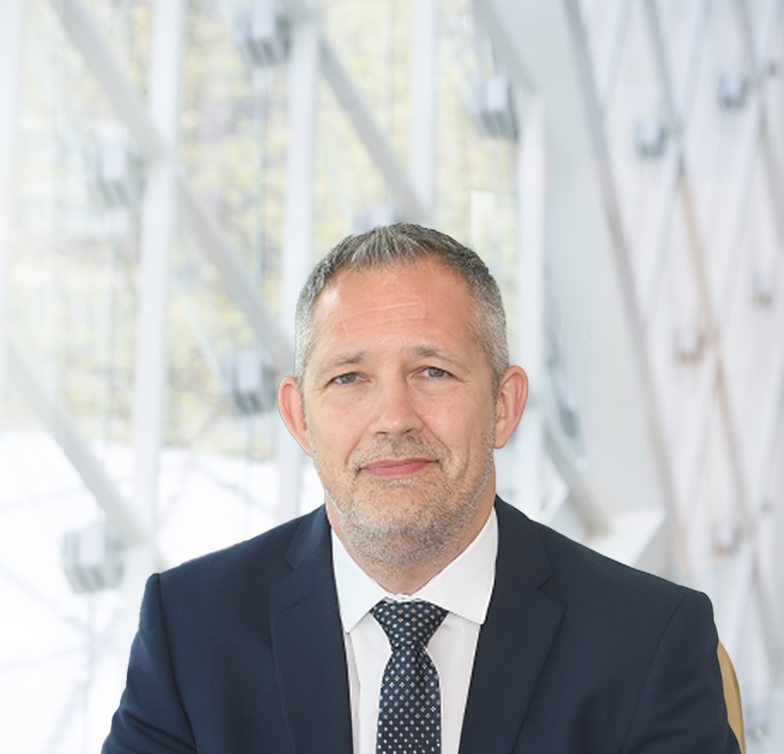
Fraser Paget
Our latest survey of 500 mid-sized business leaders highlights that mid-sized businesses are bracing for a challenging start to 2025, with supply chain pressures and rising costs topping their list of concerns. Almost half (47%) of mid-sized companies are looking to integrate AI into their supply chain operations to streamline processes, reduce errors and improve overall efficiency.
The insights in this article are from a series of interviews with our experts about key supply chain areas they believe businesses will prioritise in the coming year to build more resilient supply chains.
Extracted from an interview with James Egert, Partner
The regulatory landscape is becoming increasingly complex, and as a result, more businesses are facing disruption, fines and reputational damage from non-compliance. With certain legislation impacting businesses of all sizes across every sector, it is important to get to grips with what they mean for your business.
Two key pieces of legislation, the Criminal Finances Act 2017 and the Economic Crime and Corporate Transparency Act 2023, are making it significantly more important for businesses to prevent being unknowingly involved in financial crime. This legislation requires increased transparency around financial and wider business processes, while also introducing new offences for businesses who fail to have sufficient safeguards in place to prevent fraud.
More businesses are also facing questions from external stakeholders specifically about how they are responding to the Corporate Criminal Offence (CCO) legislation (part of the CFA 2017). This is particularly important for those businesses planning or undertaking a transaction, as we have seen deals stall because issues relating to a lack of CCO process were uncovered during due diligence. This shows it is not just about prosecutions or having a defence, but how staying up to date with the latest regulations can have a material impact across different areas of your business.
Staying aware of current and future legislation and regulatory changes can help you stay ahead of any future challenges and ensure you are acting compliantly across your supply chain.
Subscribe to our Supply Chains newsletter to stay up to date with evolving regulation and compliance challenges.
Extracted from an interview with Fraser Paget, Head of Supply Chain & Logistics Services
Many businesses need to take a more holistic view of their supply chain, identifying silos and opportunities for optimisation from end to end. By evaluating every stage of the supply chain – from sales and operations planning processes through to purchasing and procurement – businesses can get a better understanding of areas for improvement, such as supplier reliability and the effectiveness of sustainability measures.
When it comes to your suppliers, if you are reliant on a sole supplier for certain materials or products, it is important to prioritise taking a closer look and understanding if they have robust continuity plans to avoid disruption. Without the right stock at the beginning of the supply chain, you risk facing issues across the rest of your supply chain. And it is challenges like this that highlight the need to evaluate every stage of the supply chain to ensure end-to-end resilience.
In the longer term, having full visibility and sufficient data about your supply chain can help you make informed decisions as early as possible and minimise any future disruptions.
Extracted from an interview with Fraser Paget, Head of Supply Chain & Logistics Services
A digital transformation typically incorporates every area of the supply chain, including people, systems and processes – and within these, businesses are having the most issues when it comes to change management and IT integrations. Working with legacy data across different systems cause migration issues and often businesses do not plan enough or allocate enough time into testing or resources into dedicated project management. When implementing change, it is crucial businesses consider their supply chain and the impact transformation may have on data accuracy, inventory levels and ultimately availability of components or finished goods.
The more efficient and cost-effective you can make your supply chain as part of your digital transformation, the better the business result. By integrating technology across your supply chain, or automating certain elements such as forecasting, transport, inventory/warehouse management or materials ordering, you can more effectively understand your end to end cost that will better inform purchasing decisions – ensuring you have availability that meets customer demand.
Extracted from an interview with Matthew Clark, Partner, Customs, Excise & International Trade
It goes without saying that there has been an unprecedented level of international trade and supply chain disruptions in recent years. In some cases, these disruptions have meant businesses are unable to get the goods they have ordered, or they have faced increased transport, customs clearance or indirect tax costs. This is where examining and understanding international trade customs supply chain data can help – making it easier to predict potential risks, minimise disruptions and optimise indirect tax (customs duty and import VAT) on your imported goods.
Our Building Supply Chain Resilience webinar series offers valuable insights into the challenges businesses face in maintaining robust supply chains, along with effective strategies to help you assess and manage risks, fortifying your supply chain against disruptions. Watch past webinars and register for upcoming ones here.
However, many businesses are finding it hard to identify actionable insights because of the sheer amount of international trade data they have internally or receive from a tax authority. A lot of businesses are still using Excel to manage international trade data despite there now being more sophisticated software and data analytics tools out there. If you have a data analytics dashboard with a global map that shows your goods moving from A to B with hotspots and opportunities highlighted and colour-coded data, you are going to find it much easier to spot risks and opportunities, and effectively communicate these within your business.
Ultimately, data analytics does not have to be daunting or expensive. There are tools on the market that can help you analyse and understand your data, so you can better navigate supply chain disruptions and optimise indirect tax costs within your supply chains.
Sign up for demonstration of our Customs Data Analytics Tool which provides expert insights on compliance risks and indirect tax optimisation within your supply chain.
Extracted from an interview with Richard Austin, Head of Value Creation Services & Manufacturing
The adage 'Cash is king' has never been more apt. Building resilience in your supply chain to respond to the regulatory and economic challenges typically requires both cash focus and investment. However, high interest rates and inflation are forcing many businesses to look internally for this investment, focusing on cash culture, processes, and training to generate cash and efficiencies within their end-to-end supply chain management.
The key to success is full transparency of financial and operational performance across your supply chain, from sourcing suppliers/materials to final delivery. Once you have a detailed understanding, identify areas where cash is being tied up and where you have gaps, for example, your supplier negotiation strategy (cost-vs-cash balance), opportunities for automation, or SKUs if you're holding excess stock.
As part of this, traditional silos between procurement, operations and finance need to be broken down to ensure a unified approach – balanced scorecards of KPIs and shared objectives can help create a more cohesive strategy for managing cash flow and working capital.
Ultimately, having a well-integrated supply chain can enable you to manage your working capital more effectively by ensuring you have the right product in the right place when you need it. Regular stock counts, supply chain management automation and ensuring you have a robust supply chain strategy can help you optimise inventory levels and achieve a well-managed cash position.
Get expert tips on managing your cashflow – sign up for supply chain insights.
Extracted from an interview with Frederic Larquetoux, Client Service Partner, Financial Reporting & Corporate Reporting Advisory
Now more than ever, investors, customers and employees are expecting businesses to prioritise ESG across their supply chain. Supply chains are often responsible for a significant portion of a company's environmental footprint and, therefore, are an area where businesses must take direct action to reduce their impact.
Businesses are increasingly being asked to demonstrate their ESG credentials to be able to continue to trade with other companies. Those with strong ESG credentials are even gaining access to new markets and opportunities, as investors increasingly favour more environmentally conscious businesses.
Essentially, being transparent about your supply chain sustainability efforts and providing clear environmental reporting is important for building credibility and trust in your brand.